Replacement Windows for Improved Energy Efficiency: A Walk-Through Case Study
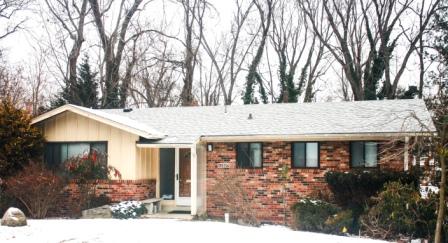
I'm not a building inspector, but as a former
building contractor and a widely published home-improvement writer, I'm often
asked by friends and acquaintances to assess their homes and suggest the best
ways to address whatever issues there might be. My friend Tony—a person driven
chiefly by a desire to responsibly fulfill his duties as a family man—recently
presented me with an interesting case.
Tony and his wife, Karen, had been given
stewardship of a 1950s rambler in an upscale suburb of Washington, D.C., that
belongs to her 85-year-old father. It's modest by any measure except for its
value—$450,000 to $500,000 in today's market—and in need of some TLC. The
father is alive and well but living elsewhere. He doesn't need to recover
equity or earn income from the house—it'll one day be part of his legacy to his
daughter and grandkids—but he doesn't want the headaches of caring for it,
either. That falls to Tony, and he's asked me what he needs to do to preserve
the value of the house.
For the time being, Tony is letting one of
his daughters—a recent university graduate—live in the house with friends until
she gets a footing in her career (and with a B.A. in Cultural Anthropology, it’s
anyone’s guess as to how long that will take).
The young woman had mentioned more than once during this unusually cold
D.C. winter that the house is chilly.
Tony's focus is on the windows. Most of them
are horizontal sliders. The living room also features two sliding-glass doors—a
kind of glass wall that overlooks a rustic backyard. Should he replace any or
all of them?
During my walk-through, I encountered 12
single-glazed, aluminum-frame horizontal sliders of 1970s vintage—not the best
from a comfort or energy standpoint, but their factory finish is still in
pretty good shape, and they're fitted with screens and storm sashes. The
exterior caulking around the frames is fairly worn out and cracking.
On my way inside, I noticed that the soffit
panels at the eaves have all been taken off. I saw that the underside of the
sheathing is water-stained. I'll bet there was leaking from ice damming (thick
ridges of ice along the eaves), and it’s ruined the soffits. Tony's already had
a new asphalt shingle roof put on. I
hope they flashed the eaves against leakage caused by ice dams.
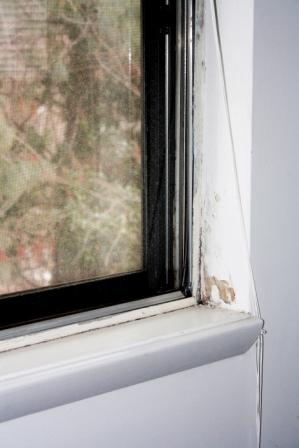
Looking at the windows from inside, I found
some evidence of moisture infiltration around the jambs and sills. Was the
source the damaged caulk? Inadequate
flashing in the original installation? Leaks
from ice dams?
Better windows are available these days. In
our market, it would probably cost him about $1,000 apiece to replace the
sliders with vinyl low-E, gas-filled units. There's also a big combination unit
with fixed glass and double-hungs on the front of the house; replacement would
cost about $2,000. But would replacement windows—properly installed—actually
improve comfort, and preserve or add value to the house?
While mulling that over, I went into the
living room to look at the sliding glass patio doors. They’re much newer than
the other windows, as they have aluminum frames and insulating glass. They’re
in great shape, but the sheer size of the glazed area explains why the house is
so chilly in winter.
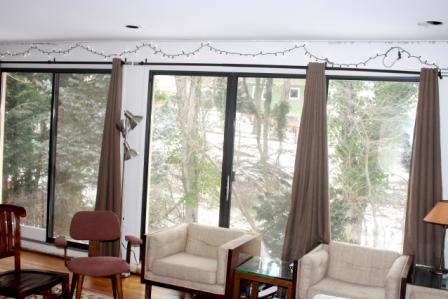
And there’s another issue: the living room is above a walk-out basement,
so the door sills sit about 9 feet above the grade of the stone patio below,
which is a code violation. Tony would never be able to sell or rent out the
house without addressing that problem.
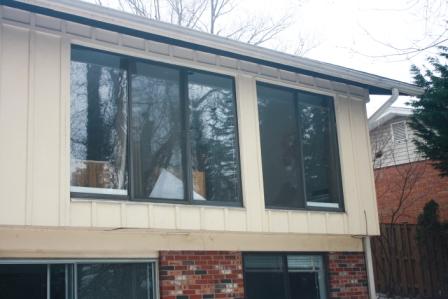
The Remodeling Magazine’s 2015 Cost vs. Value
Report states that the return on resale for vinyl replacement windows in the
South Atlantic region area is about 60%.
My advice to Tony is this:
- It
wouldn't make much sense to replace the horizontal sliding windows
throughout the house. While they're old and only single-glazed, they're
fitted with storm sashes, so their energy performance is roughly
comparable to double-paned glazing. I have concerns about the evidence of
moisture infiltration around the windows, but my guess is that the new
roof may have corrected the problem. I would, however, renew the exterior
caulking, and fill and paint the interior finished openings, as well as keep an
eye on them to see whether evidence of moisture intrusion returns.
- It wouldn't make any sense to replace the sliding glass doors in the living room with new ones of comparable size. It would cost about $5,000 to upgrade them with doors with gas-filled glazing, and that would improve the energy performance from R-2 to R-4, but it would result in only a very small improvement in comfort, and probably no reduction in energy costs. Plus, he'd still have the code issue to deal with.
However, there are a number of ways to address the code issue:
- To simply remove the violation, install approved guardrails at least 48 inches high, and align them with the sliding door sills.
- To remove the violation and improve comfort, take out the sliding glass patio doors and redesign the wall by reconstructing it with better insulation and smaller windows.
- To remove the violation and add value to the house, add a deck off the living room.
The Cost vs. Value Report says that in the Washington, D.C., area, a deck addition returns almost 96% of its cost at resale.